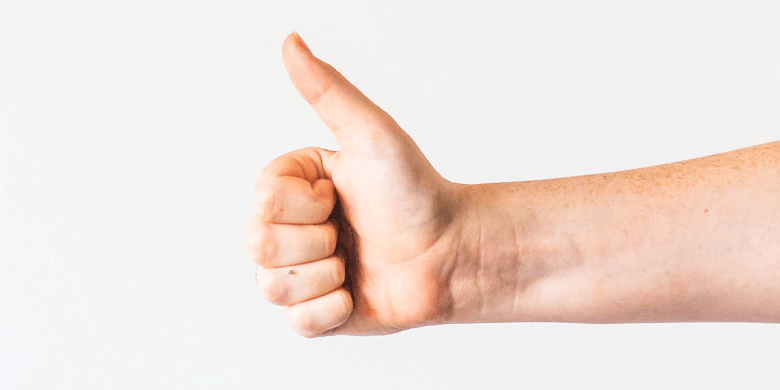
5 May, 2022
Quality Control For Lanyards And What To Look For
Quality control is a bit part of the production process for any product, so we wanted to run through some of the important aspects of quality control that we run through at lanyardsonly.com.au and explain what may occur when purchasing from other companies.
Once a mistake has been made, you usually can’t rectify it on the order provided. It would need to be rerun. If you do not order lanyards from us, but order from another company we want to explain some of the common issues and why they occur so you have a better knowledge of why the problem happened. This hopefully will help you in your complaint to the company and get a resolution to the issue quicker and more to your satisfaction.
1. Material
This is obviously a big one as it is what the print will be applied to, along with how durable and long-lasting your lanyard will be. A lanyard starts life out as being yarn on a roll. A lanyard weaving machine is used to make the final lanyard material. Up to 20 different rolls of yarn are put onto the machine and it then weaves them together to make the lanyard. There are two things that can happen in this process. Firstly, the factory may use cheaper and inferior yarn. If this is the case, the lanyard may start to fray after only several uses. The other issue is they do not use 20 rolls, but rather they use less, making it a more open weave. The danger with this is the open weave will affect the print quality. It will also make the lanyard weaker in construction. For our lanyards, we always try to achieve the tightest weave we can and only use good quality yarn.
2. Print Peeling Off
There can be several reasons for this. First, it depends on what type of print you have on the lanyard. Some factories will do screen printing and others use a transfer method. When using a transfer, they need to apply glue first to the lanyard. The transfers are then applied on top. If the factory uses poor quality glue, the transfer can begin to peel off the lanyard. In regards to screenprinting, the main issue is if the ink is not cured properly. After printing, the ink needs to dry and cure onto the lanyard. If this is not done, the ink can peel or “rub” off. The lanyard needs to go through a heat press at a high temperature for a set amount of time. Some factories try to rush this and don’t allow enough curing time. Also, they need to factor in the local weather conditions. If it is cold and moist, they need to allow additional time for curing, otherwise, the ink will not hold. Generally, this is the most common issue. Our factory has been producing lanyards for over 40 years, so we have the experience to know how much to properly cure the material for.
3. Stitching
The stitching part is where the different connectors or fasteners are added such as the clip at the bottom of the safety breakaway on the side. If a lanyard is poorly stitched it will not last. The fastener will come loose and potentially break off the lanyard. Stitching is vitally important when the attachment you want is going to carry a weight load such as keys. The main reasons for poor stitching are either poor oversight from the factory or the workers being pushed too hard to stitch too many lanyards in a given time frame. We always ensure there are enough workers on staff at any time, so the quantities required are reasonable.
The above are the 3 main factors you will come across with quality issues in lanyards. Rest assured we have been doing this for over 20 years and have worked with the same factory all of that time. This ensures the best quality control. Sometimes things will still occur, as it is a manufacturing process, but we will always actively engage with customers to come up with a solution quickly.
The Lanyards Only Team